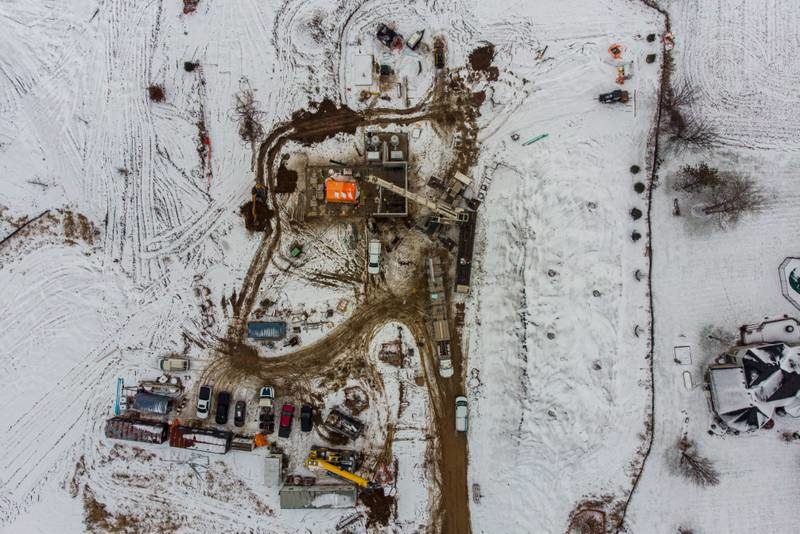
How to Continue Concrete Projects in Winter
When you’re working on any construction project, you don’t want unexpected stoppages and delays due to extreme cold. Months with tools and equipment lying idle translates into lost revenue that cannot be recovered. While some activities – like planning or internal construction – can continue in the winter, several aspects are hampered by inclement weather. None more so than pouring and curing of concrete on site. Since cast-in-place (or site-cast) concrete, masonry and cladding rely on moderate temperatures to cure properly, you can’t pour it outside when temperatures drop too low, which they do in Ontario for many months of the year. No one wants to pause construction all winter, but what’s the alternative when concrete is a crucial element to most construction projects? Read on and we’ll show you how precast concrete will keep your construction project on track even in the harshest winter.
Curing Cast-in-place Concrete
Ideal temperatures for curing concrete are between 4 and 15°C. If you use cast-in-place concrete in temperatures lower than this you risk:
- Concrete freezing before it gains strength, extreme freezing can permanently damage the matrix
- Concrete setting more slowly: the hydration reaction stops and the concrete doesn’t gain strength until temperatures increase
With Ontario temperatures ranging from -3 to -19°C December to February, that’s three months of not being able to pour concrete on your work site. November, March and April don’t guarantee warm enough temperatures, so winter concrete and heating are needed for nearly six months of the year.
It’s not just the cold which impacts pouring and curing. There are many weather variables which affect the curing process of concrete. Precipitation impedes the curing (and pouring of) concrete. You can’t pour concrete outside in the rain! Snow and ice can also close down a job site, for practical or safety reasons.
The Hidden Cost of Cast-in-place Concrete
When you use cast-in-place concrete in the winter, there are several adaptations you have to make, all of which add up to extra cost, equipment and time.
- Concrete work needs to be tarped and heated, which can be expensive to set up and maintain. The same goes for masonry, clay and brick work, which is one reason why Modular Buildings are an excellent choice.
- You’re forced to rely on accelerators and additives to assist with the setting and curing of the concrete.
- Raise the ambient temperature – for example by putting up a temporary structure around the concrete – or to thaw the ground. These measures are time consuming, expensive and inefficient in extreme cold.
Other challenges with cast-in-place:
- Cast-in-place can be time consuming as moulds have to be created on site, before pouring can begin.
- It takes longer to close a project as the cast-in-place set up and pouring takes longer.
- You have to budget for higher labour costs due to extra steps in creating the molds and pouring the concrete on site.
Thankfully, though, there is a better solution: Precast Concrete.
Advantages of Precast Concrete for Winter
Precast concrete is made in a factory, with a closed, climate-controlled environment. All of the mixing, pouring and curing is done inside, all year round. You order the units you need and have them delivered to your site.
This means you can continue construction all year long, regardless of the winter weather. We maintain a consistent temperature inside our plant, meaning we can be sure concrete will cure and set in a given time frame, and that it will reach the required strength. Every time. You present us with your design needs, then we create the concrete products you need using standard or custom moulds.
Aside from being able to continue construction in the middle of a harsh winter, there are many supplementary benefits to precast concrete:
- Consistent curing, strength and quality, thanks to the fact that the concrete is poured in a climate-controlled factory environment. Heat can be as much a challenge as cold, so we keep temperatures optimum for successful curing.
- Consistent finish. Again, the controlled temperature means that each piece cures and sets at the same rate, resulting in a consistent finish. This gives you a more professional, aesthetically pleasing, architectural look.
- Precision. The use of moulds in an internal setting ensures that each unit can be poured with higher precision and accuracy compared to on-site.
- Control of your timeline. Since you don’t have to wait for concrete to cure on site, you can accurately plan when to receive the concrete units, how long you’ll need for installation, and when you can continue to the next phase of your build.
Read our blog post, Why you Need Precast Concrete for your Project to learn more.
With challenges like variable outside temperatures and conditions, it could be tempting to plan your construction schedule so that you’re not pouring concrete on site during the cold winter months or inclement weather. However, this is no longer a restriction with precast concrete. You can order units to be made at any time in the year, thanks to a controlled factory environment, meaning you can accurately predict and manage your construction schedule all year long.